Supporting building maintenance using a databaseFacility Management System
- Infrastructure
- IT & DX
- Maintenance & Management
We offer a service to streamline facility inspections using mobile tools and automate inspection data input through data linkage. This will improve long-term repair plans by establishing an information infrastructure through the unification of BIM models and the facility registry. The accumulated data can also be used to carry out digital on-the-job training, thereby revitalizing your company as a tool for passing on technical knowledge.
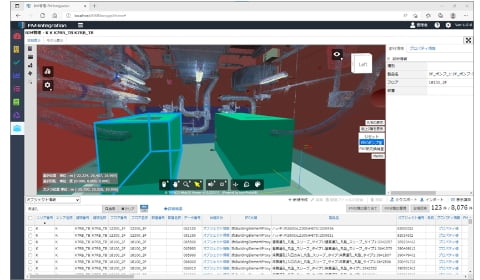
Point
- Visualizing maintenance plans
- Connecting diagrams (PDFs) and a facility registry
- Easily inputting maintenance records on site
- Streamlining inspections
We can solve these problems!
- Data isn’t organized in a uniform method, so it takes time to find data on buildings or facilities.
- You would like to manage data, including failures that occurred on site as a database.
- You would like to automate manual work due to a labor shortage.
Overview of Our Technology and Services
- We streamline facility inspections using mobile tools and automate inspection data input through data linkage.
- The service will improve long-term repair plans by establishing an information infrastructure through the unification of BIM models and the facility registry.
- The accumulated data can also be used to carry out digital on-the-job training, thereby revitalizing your company as a tool for passing on technical knowledge.
-
- We provide support for introducing the system.
- ・Establishing a web server and the system
- ・Installing the system on your devices
- ・Registering existing maintenance data in the database
- ・Creating a facility maintenance registry
- Reducing work hours for inspection
- Training employees with the system
- Digital on-the-job training
- Passing on technical knowledge
- Cooperation between business sites
- Revitalizing the company
Visualizing maintenance plans
Using the accumulated data in the system, you can compare and consider more efficient repair plans, thereby reducing maintenance costs in the medium to long term.
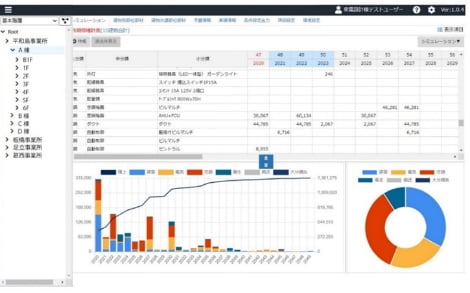
Connecting diagrams (PDFs) and a facility registry
By connecting diagrams (PDFs) and a facility registry, information can be centrally managed, which reduces time spent searching for data. The system also accumulates information on failures, so problems can be solved quickly.
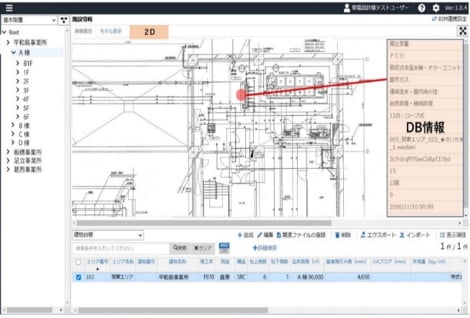
Easily inputting maintenance records on site
Mobile tools such as tablets can be used to quickly and easily input maintenance records into the system. In addition, current records can be compared with previous ones, and if there are any abnormalities in the inspection data, the system will alert the user.
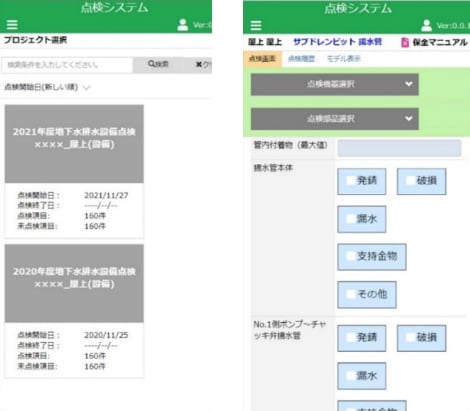
Streamlining inspections*Under development
Individual QR codes ensure that you won’t recognize the wrong device.
There is also no need to add up totals after returning to the office, which reduces manhours and prevents the input of incorrect data.
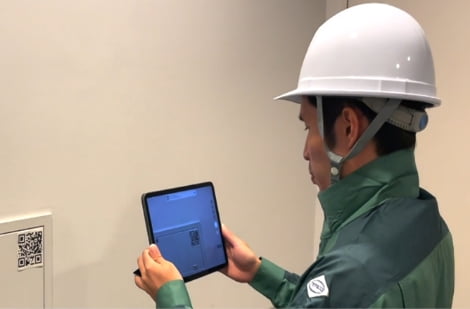
Track Record
We have received inquiries from companies that manage infrastructure facilities or plants for introducing this system.
【Examples of companies】
- Tokyo Electric Power Company Holdings and other electric companies
- Trading companies
Form of Service Provision
We will provide an estimate after talking with you.